Aluminium profile price list
Aluminium profile price list
Aluminium is a versatile and widely used metal, with applications ranging from aerospace engineering to food packaging. It is prized for its lightweight, strength, and corrosion resistance. The aluminium manufacturing process pdf outlines the various stages involved in producing this metal, from mining the raw materials to shaping and finishing the final product.
Mining and refining
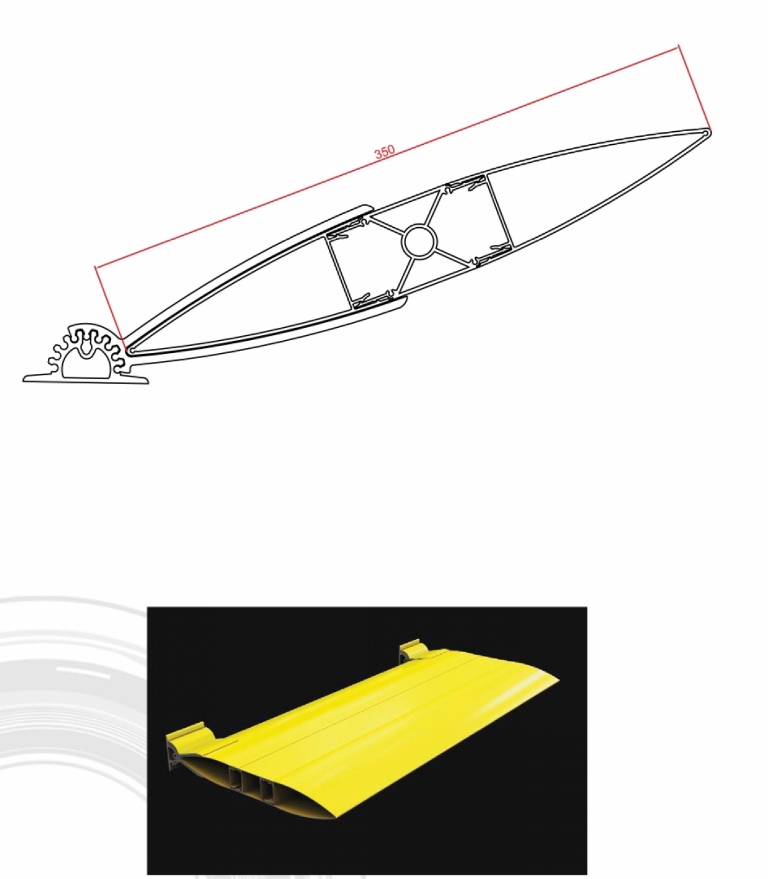
The first step in the aluminium manufacturing process is the extraction of bauxite, the primary ore used to make aluminium. Bauxite is typically found in tropical and subtropical regions, and is mined using open-pit mining techniques. Once the bauxite is extracted, it is transported to a processing plant where it undergoes a series of refining steps to produce alumina, or aluminium oxide.
The refining process begins with crushing the bauxite into small particles, typically less than one centimetre in size. The crushed bauxite is then mixed with a hot solution of caustic soda, which dissolves the alumina and leaves behind the impurities. This process is known as the Bayer process, named after the Austrian chemist who developed it in the late 19th century.
The resulting solution of alumina and impurities is then filtered and heated to remove the water and any remaining impurities. The resulting solid alumina is then transported to smelters where it is converted into aluminium metal.
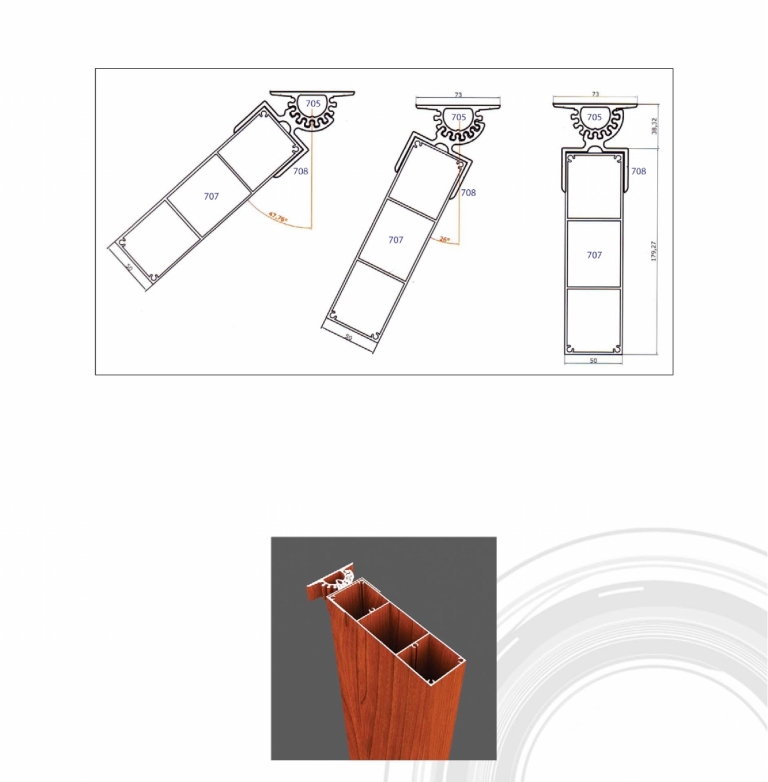
Smelting
The smelting process involves the conversion of alumina into aluminium metal. This process takes place in large industrial furnaces known as electrolytic cells. The cells are made of steel and lined with carbon to provide electrical conductivity.
The cells are filled with a molten mixture of alumina and cryolite, a mineral that lowers the melting point of alumina and improves its electrical conductivity. An electric current is passed through the mixture, causing the alumina to break down into its component parts: aluminium metal and oxygen gas.
The oxygen gas reacts with the carbon lining of the cell to form carbon dioxide gas, which is released into the atmosphere. The aluminium metal sinks to the bottom of the cell and is periodically drained off, typically every 24-48 hours.
The drained aluminium metal is known as primary aluminium, and typically contains 99.5% pure aluminium. It is then transported to processing plants where it undergoes further refining and shaping.
Refining and shaping
The refining and shaping of aluminium involves a series of processes designed to improve its mechanical properties and prepare it for use in various applications. The first step is to melt the primary aluminium in large furnaces. The molten aluminium is then poured into ingot molds to cool and solidify into large blocks of metal.
The ingots are then transported to rolling mills where they are flattened into sheets, typically less than one centimetre thick. The sheets are then coiled and transported to factories where they are used to make a wide variety of products, including cans, car parts, and building materials.
Some of the most common techniques used to shape aluminium include extrusion, forging, and casting. Extrusion involves forcing the metal through a die to create a specific shape, such as a tube or rod. Forging involves shaping the metal by applying pressure with a hammer or press, typically used to create high-strength components such as aircraft parts. Casting involves pouring molten aluminium into a mold to create a specific shape, typically used to create intricate or custom parts.
Finishing
The final stage in the aluminium manufacturing process is finishing, which involves a variety of processes designed to improve the appearance and performance of the metal. Some of the most common finishing techniques include anodizing, painting, and polishing.
Anodizing involves creating a thin layer of oxide on the surface of the metal, which can be colored to create a wide range of finishes. This process improves the metal’s resistance to corrosion and makes it more durable. Painting involves applying a coating of paint to the surface of the metal, which can be customized to match a specific color or design. Polishing involves using abrasive materials to smooth the surface of the metal, creating a shiny and reflective finish.
Another important finishing technique is heat treating, which involves heating the metal to a specific temperature and then cooling it rapidly, often with water or oil. This process can improve the mechanical properties of the metal, making it stronger and more resistant to wear and tear.
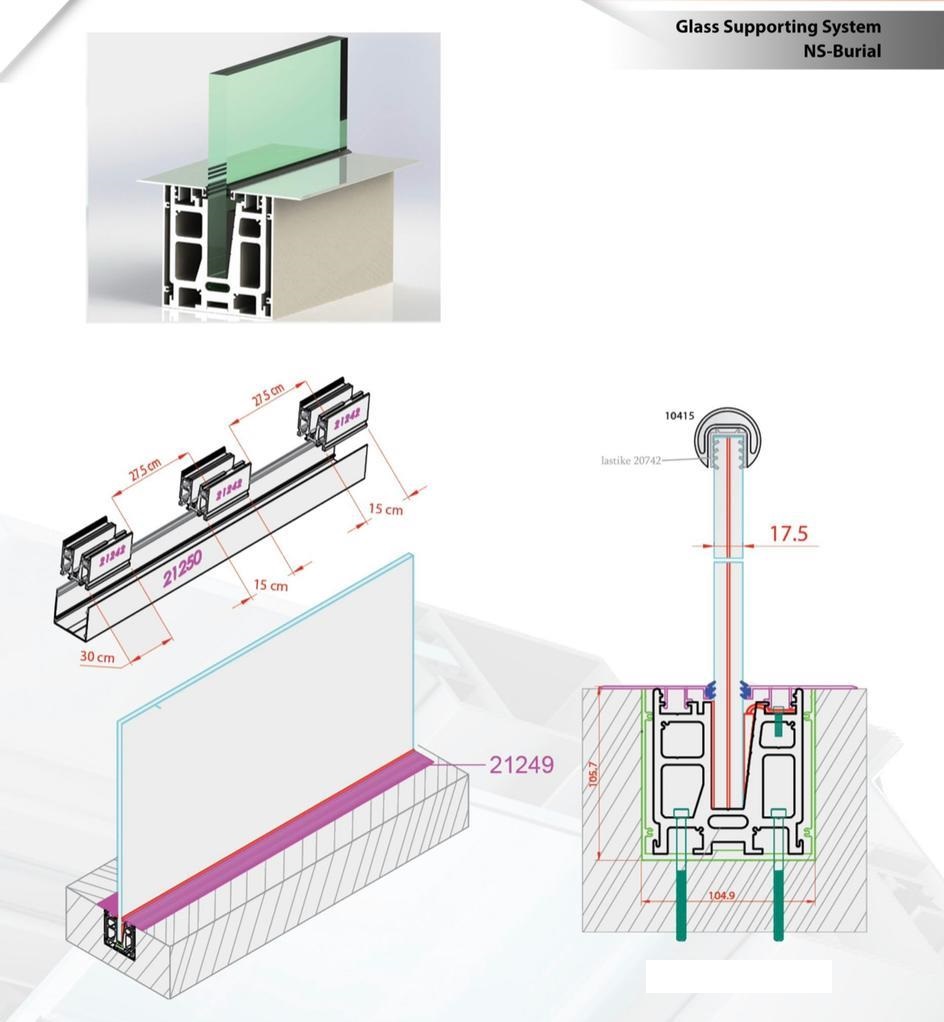
Conclusion
The aluminium manufacturing process pdf outlines the various stages involved in producing this versatile and widely used metal. From mining and refining bauxite to smelting and shaping aluminium metal, the process involves a range of techniques designed to produce high-quality products that meet the demands of modern industry.
The aluminium industry continues to evolve and innovate, with new techniques and technologies emerging to improve the efficiency and sustainability of the manufacturing process. As the demand for lightweight, durable, and corrosion-resistant materials continues to grow, aluminium is sure to remain a key player in the global manufacturing industry for years to come.
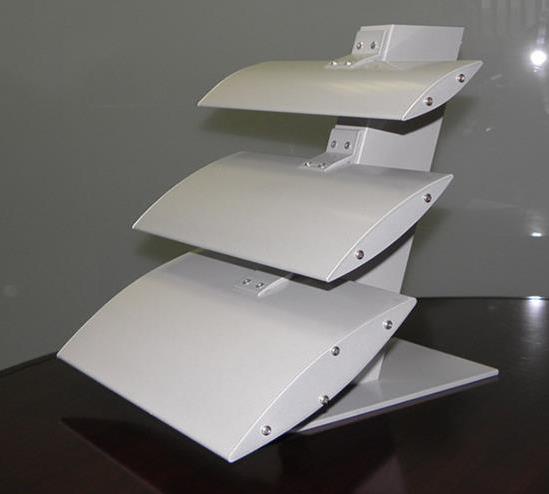
Aluminium profile price list Aluminium profile price list Aluminium profile price list Aluminium profile price list